Complete the form below to receive a custom quote from our Public Safety Sales team. You'll hear from us typically within the hour. We look forward to helping you!
Safer, Smarter Line Inspections
Powerline Inspection Drones
Unmanned Aerial Systems purpose-built for aerial power line inspection give utilities, inspection firms, and contractors the high-resolution visuals, thermal data, and 3D models they need in minutes—while keeping crews safely on the ground. By swapping helicopters and bucket trucks for agile powerline inspection drones, organizations cut costs, minimize outages, and detect faults before they become failures.
Missions that keep power flowing
Why Use Drones for Powerline Inspections?
Aerial power line inspection with utility drones replaces hazardous climbs and costly helicopter patrols with rapid, repeatable data capture.  
-
Enhanced Worker Safety:
Powerline inspection drones let crews gather high-resolution visuals and thermal data from the ground, eliminating dangerous climbs and costly helicopter flights—“a safer, faster, and more precise approach” than traditional methods. -
Accelerated Inspection Cycles:
One power company's three-person UAS team averaged 14 miles of line per day—inspecting 7,000 structures in eight months with about seven minutes per tower. -
Superior Data & Early Fault Detection:
Automated flights capture repeatable RGB, thermal, and LiDAR imagery, enabling daily patrols that flag hotspots or cracked hardware long before failure.  -
Cost Savings & ROI:
By replacing ground crews and manned aircraft, Georgia Power cut annual inspection costs by roughly 60 percent while uncovering over 4× more critical issues than traditional methods.
Aerial Insights, Safer Outcomes
Use Cases for Powerline Inspection Drones
Visual Inspections
Drones perform thorough aerial power line inspections, capturing detailed imagery while improving safety and efficiency.
- High-Resolution Imagery: Drones capture close-up photos of wires, insulators, and components, revealing corrosion, cracks, or wear.
- No Shutdown Inspections: Perform regular visual checks without cutting power or sending crews up towers, minimizing disruption and risk.
Fault Detection
Inspection UAVs provide proactive fault detection, identifying anomalies before they lead to outages or safety hazards.
- Thermal Hotspot Detection: Infrared-equipped drones spot overheated components or loose connections, enabling repairs before failures or fires occur.
- Outage Prevention: Early fault detection enables repairs before failures, reducing unplanned outages and improving grid reliability.
Vegetation Management
Utility drones streamline vegetation management, surveying power line corridors for encroaching foliage to prevent outages.
- Encroachment Monitoring: Aerial surveys identify trees and vegetation nearing power lines, guiding timely trimming to prevent service disruptions.
- Wildfire Prevention: Early detection of vegetation hazards reduces fire risks by ensuring power lines are clear of overgrowth.
Storm Damage Assessment
Drones enable rapid storm damage assessment, allowing utility teams to safely evaluate outages and expedite power restoration.
- Rapid Damage Survey: Quickly evaluate damage to power lines and poles after storms, identifying downed lines and hazards for swift repair planning.
- Accelerated Restoration: Drones provide detailed damage data to help utilities dispatch crews efficiently, speeding up power restoration and boosting grid resilience.
3D Modeling
Drones provide precise 3D modeling of power infrastructure, generating digital twins that aid in engineering analysis and future planning.
- Digital Twin Creation: Drones capture images for photogrammetry, producing 3D models of towers and lines for detailed visualization and planning.
- Engineering Analysis: Accurate 3D models aid engineers in simulations and upgrade planning without the need for time-consuming on-site measurements.
Structural Integrity Assessments
Drones conduct detailed structural integrity assessments, inspecting towers and lines for wear or damage to inform proactive maintenance decisions.
- Close Structural Inspections: High-resolution drone imagery reveals fine details on towers, poles, and hardware, highlighting rust, cracks, or other damage.
- Predictive Maintenance: Routine drone monitoring of structural conditions supports data-driven maintenance schedules, fixing issues before they escalate.
Find the right UAS for your operations
Powerline Inspection Drone packages
We have a wide variety of enterprise drone solutions to help you and your team accomplish your jobs quicker and easier. see our recommended drone packages below or give us a call and get a customized quote for your needs.
Matrice 350 RTK
Fully Powered to Forge Ahead.


An upgraded flagship drone platform, the Matrice 350 RTK sets a new benchmark for the industry. This next-generation drone platform features an all-new video transmission system and control experience, a more efficient battery system, and more comprehensive safety features, as well as robust payload and expansion capabilities
- Up to 55 Minute Flight Time
- 20km Max Transmission Range
- Multiple Cameras
- Higher Payload Compatibility
DJI Matrice 4 Thermal
The Age of Intelligent Flight.


Experience unmatched thermal imaging and intelligent AI capabilities with the DJI Matrice 4 Thermal, designed for precision and performance in challenging environments.
- Ultra-High-Resolution Thermal Imaging
- 112x Hybrid Zoom
- Advanced AI for Real-Time Detection
- 49-Minute Flight Time
- Enhanced Low-Light Operations
Matrice 30T
Power in Portability.
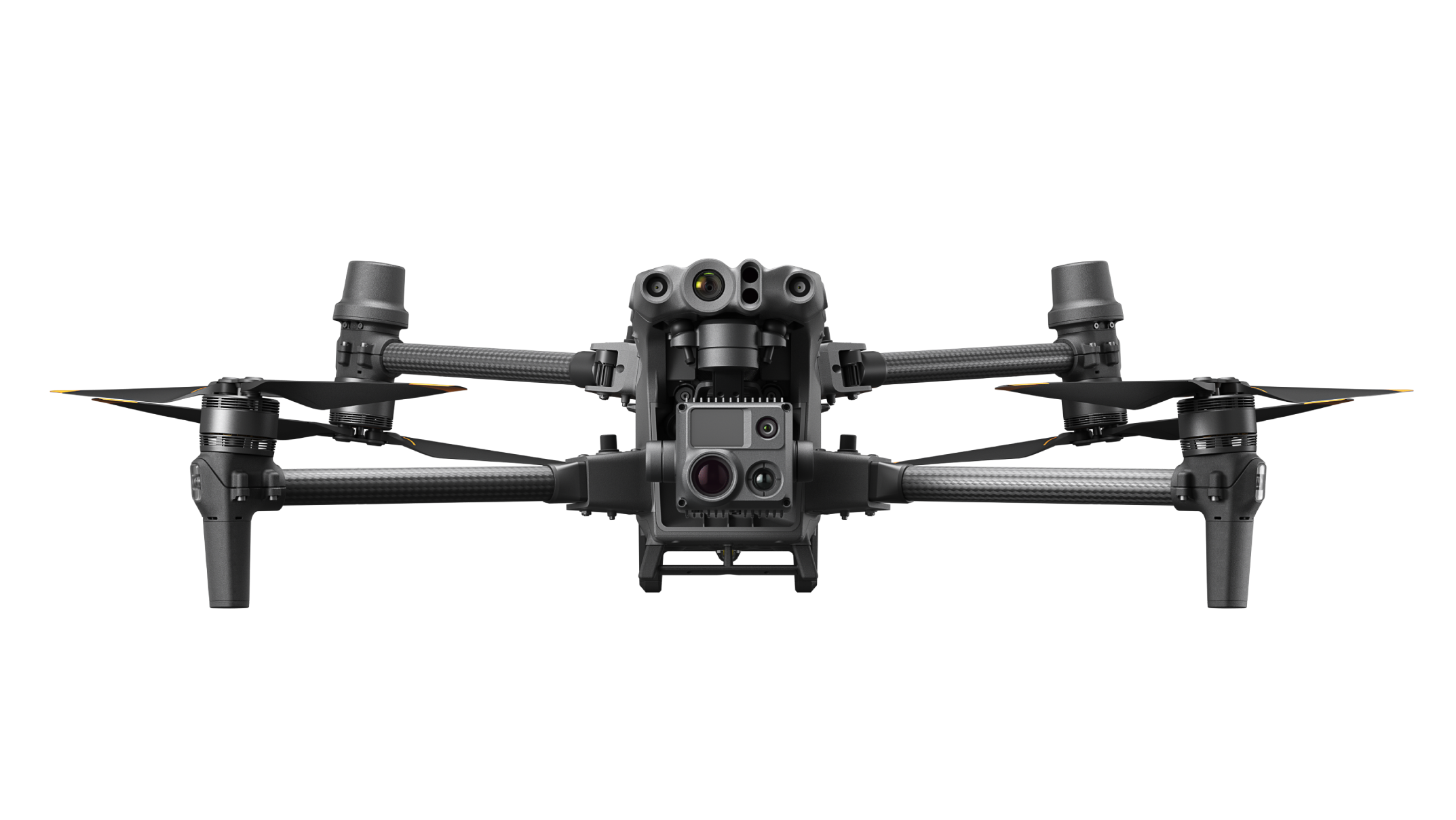
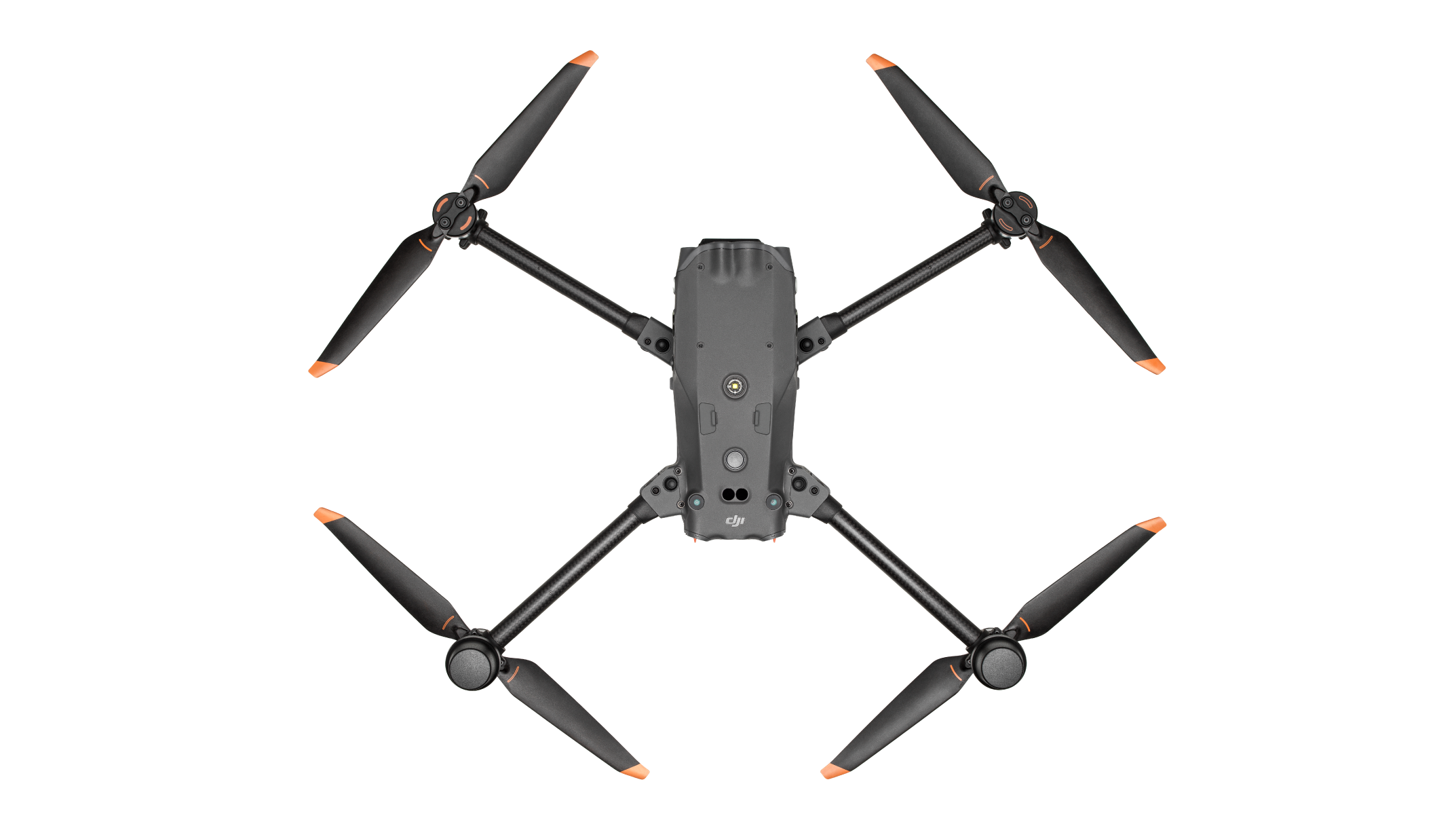
One of DJI's most popular flagship models, the M30T is a weatherproof drone that fits in a backpack and integrates multiple high-performance sensors into one highly capable platform.
- 41 min Flight Time
- 640 × 512 px Thermal Camera
- 12 MP Wide Camera
- 48 MP Zoom Camera
- 5x-16x Optical Zoom
- 0.75 mi. Laser Range Finder
- IP55 Weather Protection
EVO Max 4T XE
Reach New Frontiers.


A feature-packed drone with a 640x512 thermal sensor, 160x hybrid zoom, 10x optical zoom, laser rangefinder, and 4K wide camera. With a flight time of up to 42 minutes and a range of up to 12.4 miles thanks to the SkyLink 3.0 transmission system, it's a choice public safety solution.
- 42 Minute Flight Time
- 640 x 512 Thermal Sensor
- 10x Optical Zoom
- Laser Rangefinder
- 12.4 Mile Transmission Range

Teledyne FLIR SIRAS
Professional Drone With Thermal and Visible Camera Payload


The Teledyne FLIR SIRAS is an IP54-rated professional drone with interchangeable payloads, high-quality visible and thermal imaging, secure onboard data storage, front collision avoidance, and hot-swappable batteries for extended missions.
- 31-Minute Flight Time & Hot-Swappable Batteries
- 640 x 512 Thermal Sensor with 5x Zoom
- 16MP Visible Camera with 128x Zoom
- Front Collision Avoidance Radar up to 30m
- Secure Onboard Data Storage on microSD
- IP54-Rated for Dust and Moisture Resistance
DJI Zenmuse L2
Powerful Range, Elevated Precision


The Zenmuse L2 is a high-precision aerial LiDAR system that integrates frame LiDAR, a self-developed high-accuracy IMU, and a 4/3 CMOS RGB mapping camera. Designed for DJI flight platforms, it delivers precise, efficient, and reliable geospatial data acquisition, offering a turnkey solution for 3D data collection and high-accuracy post-processing with DJI Terra.
- Vertical Accuracy: 4 cm; Horizontal Accuracy: 5 cm without GCPs
- Exceptional Efficiency: Cover up to 2.5 km² in a single flight
- Superior Penetration: Smaller laser spots and denser point clouds for detailed mapping
- Extended Detection Range: Up to 450m at 50% reflectivity
- Turnkey Solution: One-click processing on DJI Terra for streamlined workflows
DJI Zenmuse H30T
Unparalleled Vision, Day or Night


The Zenmuse H30T is DJI’s all-weather, multi-sensor flagship payload, integrating a 48 MP wide-angle camera, a 40 MP 34× optical (400× digital) zoom camera, a 1280×1024 radiometric thermal sensor, 3 km laser rangefinder, and NIR auxiliary light. Advanced stabilization and intelligent algorithms deliver crisp, precise imaging in any environment—day or night—for public safety, energy inspection, forestry, and more.
- 48 MP wide camera & 34× optical (400× digital) zoom
- 1280×1024 thermal sensor with High-Res mode & –20 °C to 1600 °C range
- 3 km laser rangefinder for accurate distance & coordinate data
- IP54-rated & –20 °C to 50 °C operation for all-weather reliability
- 3-axis stabilization & advanced algorithms for shake-free zoom footage

Teledyne Geospatial EchoONE
Longrange and Lightweight


EchoONE is a high-precision aerial LiDAR system designed for versatility and efficiency. Weighing just 1.2kg, it seamlessly integrates with smaller UAVs, delivering long-range capabilities and exceptional accuracy. Compliant with the latest NDAA requirements, EchoONE ensures data security without compromising on affordability.
- Long-Range Performance: 270m range to 20% reflectivity targets with up to 8 returns per pulse
- Ultra-Lightweight Design: Weighs only 1.2kg, compatible with UAVs like Freefly Astro, Inspired Flight IF800, and DJI M300/M350
- High Precision: Achieves up to 1.5cm RMS vertical accuracy and 5mm ranging precision
- Accurate and Fast: Generates full undecimated georeferenced point clouds in real-time with rapid post-processing
- Integrated Colorization: Features a 5MP global shutter camera with an optional 61MP camera for enhanced imaging

Phoenix Recon-XT
Great Value Meets Great Performance


The Recon-XT is Phoenix LiDAR's ultimate value-driven LiDAR system, designed for the DJI Matrice 350 and Freefly Astro UAVs. Weighing just 1.8kg, it offers exceptional precision and long-range capabilities, making it ideal for surveying teams seeking affordability without compromising performance.
- High Precision: Achieves 2-5 cm RMS vertical accuracy at 80m with 5mm ranging precision
- Lightweight & Versatile: Weighs only 1.8kg, compatible with DJI M300/M350 and Freefly Astro UAVs
- Long-Range Performance: Operates reliably up to 80m AGL with a maximum detection range of 80m
- Accurate and Fast: Generates full undecimated georeferenced point clouds in real-time with rapid post-processing
- Flexible Mounting Options: Easily integrates with UAVs, vehicles, and mobile mapping applications

Phoenix Ranger-UAV22 Flex
Fly It, Drive It, Mount It Anywhere


The Ranger-UAV22 Flex is Phoenix LiDAR's most adaptable mapping system, seamlessly integrating into backpacks, UAVs, vehicles, and dual-head mobile scanning solutions. With a high pulse repetition rate and exceptional precision, the Ranger-UAV22 Flex is designed to meet the diverse needs of modern surveying and mapping projects.
- Ultimate Versatility: Integrates effortlessly with backpacks, UAVs, vehicles, and dual-head mobile scanning setups
- High Precision: Achieves 1.5-3.0 cm RMSEz system accuracy at 120m with 5mm ranging precision
- Long-Range Capability: Reliable operation up to 490m AGL at 20% reflectivity
- Advanced Performance: 1200 kHz pulse repetition rate and up to 15 returns per pulse for detailed and accurate point clouds
- Robust Mounting Options: Compatible with a wide range of platforms including UAVs like DJI M300/M350 and VTOL systems
Let's get your program started
Ready to build your UAS program?
Get a full, personalized system built for your specific needs. Our expert team can assess your situation, and recommend the best drone system for your organization.
Get a Personalized Quote
Powerline Inspection Drones FAQ
What is a powerline inspection drone?
A powerline inspection drone is a specialized unmanned aerial vehicle (UAV) used for aerial power line inspection. It carries high-resolution cameras, thermal sensors, and LiDAR scanners to inspect electrical lines, poles, and hardware from the air, detecting faults or hazards and collecting detailed data for maintenance.
What certifications do pilots need to fly drones for power line inspection?
In the U.S., drone pilots must have an FAA Part 107 Remote Pilot Certificate to legally conduct commercial power line inspections. Many utility companies also require additional training specific to infrastructure inspections (e.g. thermal imaging or LiDAR use) to ensure pilots can operate safely around power lines.
How much does a powerline inspection drone cost?
Prices vary widely. Entry-level inspection UAVs with basic cameras start around $5,000, while enterprise utility drone platforms with advanced sensors and software typically range from about $10,000 up to $50,000 or more. Costs increase with higher-end thermal cameras, LiDAR, and longer-flight capabilities.
Are inspection drones cost-effective?
In short, yes – deploying drones for power line inspection can significantly reduce costs and deliver a strong ROI. Replacing or augmenting ground crews and helicopter patrols with drones saves on labor and equipment; utilities have seen inspection costs drop by ~30–50% using drones. For example, Georgia Power reported about 60% annual cost savings after adopting drone inspections, along with improved data quality.
How do drones improve safety for power line inspections?
Drone inspections greatly enhance safety by keeping workers out of dangerous situations. Instead of climbing tall towers or flying in helicopters near live lines, crews can inspect remotely from the ground. Drones eliminate the need for line workers to be in hazardous areas, reducing the risk of falls, electrocution, and other accidents associated with traditional methods. By minimizing time aloft or at heights, aerial power line inspection via drone makes the job much safer.
How fast can drones inspect power lines?
Inspection drones can cover power line corridors much faster than traditional methods. In field use, a small drone team has been able to survey about 14 miles of line per day, which far outpaces on-foot inspections. Drones can cruise along lines at roughly 40 mph when needed, allowing utility crews to rapidly patrol large service areas and respond quickly after storms or outages.
What issues can drones detect during power line inspections?
Drones can spot a wide range of problems on electrical lines and towers. High-resolution visuals and sensors allow them to find things like bird nests, lightning strike damage, rust or corrosion on connectors, loose or damaged bolts, and other physical defects on poles and wires . Thermal cameras also reveal “hot spots” (overheating components) that could signal failing equipment, and LiDAR or laser measurements identify vegetation encroachment (trees too close to lines) so crews can prevent outages
What sensors do powerline inspection drones typically use?
Power line inspection drones typically use a combination of sensors to gather comprehensive data. The standard payload includes an RGB zoom camera for high-detail visual imaging, a thermal infrared camera for detecting heat anomalies, and often a LiDAR unit for 3D mapping. Using these sensors together, a single inspection UAV can capture detailed photos of hardware, identify hotspots, and map the line and surrounding terrain.
Why is thermal imaging important for power line inspections?
Thermal imaging is critical because it can detect invisible issues like overheating components. An aerial thermal camera can spot “hot” connectors, transformers, or wires that are warmer than normal – a sign of electrical resistance or fault. Catching these hot spots early allows for repairs before the part fails or potentially ignites a fire. For instance, drones equipped with infrared sensors have identified wiring hotspots that could have sparked wildfires if left unaddressed, enabling preventative maintenance and improving grid safety.
How is LiDAR used in power line inspections?
LiDAR (Light Detection and Ranging) is used to create precise 3D models of power lines and their environment. In drone inspections, LiDAR scans map the positions of wires, structures, and nearby vegetation with high accuracy. This helps utility engineers analyze pole alignments, wire sag, and clearance between vegetation and conductors. Essentially, LiDAR data allows detailed structural analysis and vegetation management planning around the line, so utilities can ensure proper line clearance and identify any physical shifts or encroachments that need attention.
Which drones are best for power line inspection?
Utilities typically choose robust, enterprise-grade drones for power line inspections. Popular models include DJI’s Matrice series (e.g., M300 or M350 RTK) for their heavy payload capacity and stability, as well as versatile systems like the DJI Matrice 4 Thermal, Autel EVO Max 4T XE, or DJI Mavic 3 Thermal for smaller-scale jobs. Fixed-wing mapping UAVs such as the senseFly eBee or Quantum Trinity are used for surveying long transmission corridors. In practice, top inspection drones like the DJI Matrice 350 RTK, senseFly eBee X, and Quantum Systems Trinity F90+ are commonly deployed – these platforms offer thermal imaging, RTK GPS precision, and longer flight times, ideal for utility work
How long can a powerline inspection drone fly on one battery?
Most high-end inspection drones have long flight endurance to cover more lines per flight. For example, the DJI Matrice 300 RTK can stay airborne for up to about 55 minutes under ideal conditions. Real-world flight times will be a bit shorter once you add payload and wind, but generally, 30–45 minutes per battery is common for enterprise utility drones. This means a single drone can inspect numerous poles or several miles of line before needing to land for a battery swap.
What software is used with powerline inspection drones?
Drone data is typically processed and analyzed using specialized software. Common drone inspection software includes mapping and photogrammetry tools like Pix4D and DroneDeploy, which can stitch images into maps and 3D models. Utilities also use inspection management platforms to organize photos of each structure, tag defects, measure distances, and generate reports. These programs help convert the drone’s raw images, thermal data, and LiDAR scans into actionable maintenance insights and documentation.
Can powerline inspection drones fly beyond visual line of sight (BVLOS)?
Not by default – FAA regulations normally require the remote pilot to keep the drone within visual line of sight. However, utilities can obtain FAA waivers or special permissions to conduct BVLOS operations in certain cases. Federal regulators have begun granting broad area waivers that allow qualified utility companies to fly drones beyond line of sight for transmission line inspections. With the right approvals and safety systems in place (such as radar or visual observers), inspection drones have even been able to cover over 120 miles of power lines in a single day by flying BVLOS. These extended-range flights greatly increase efficiency, but they require strict compliance with FAA waiver conditions for safe operation.
What are the technical challenges of using drones near power lines?
Flying close to high-voltage lines presents some technical challenges. One concern is electromagnetic interference (EMI) from the strong electrical fields, which can disrupt a drone’s compass or sensors. To counter this, inspection drones are designed with shielding and EMI-resistant electronics so they can operate reliably around live lines. Another challenge is the risk of collisions with wires or towers, especially since power lines can be thin and hard to see. Advanced inspection UAVs use AI-powered obstacle avoidance systems and multiple sensing cameras to detect and avoid obstacles in real time, helping pilots navigate safely through complex infrastructure. Operators also plan flights carefully to maintain safe distances and mitigate these risks.
Can powerline inspection drones fly in bad weather?
Enterprise drones are built to handle moderately adverse weather, but there are limits. Many inspection drones can maintain stable flight in winds of 20–30 mph and function in cold temperatures below freezing. For example, some DJI utility drones are rated to fly in conditions down to -4°F (-20°C). Light rain or mist is tolerated by certain weather-resistant models (some systems are IP-rated for water resistance), but heavy rain, snow, or lightning storms are generally avoided for safety. In practice, utilities schedule routine drone inspections for fair weather days, and only specially rugged drones like the FLIR SIRAS or others with weather-proofing are used when operations must continue in rain or high winds .
Can drones perform power line inspections at night?
Yes, but extra precautions and regulatory compliance are required. Under FAA Part 107 rules in the US, flying at night is allowed if the drone has anti-collision lighting visible for at least 3 miles and the pilot has completed nighttime operation training. In other words, the drone needs a bright strobe, and the pilot must be qualified to handle reduced visibility. In practice, most utilities conduct regular inspections in daylight hours for safety and to avoid any community concerns. Night drone flights are generally reserved for emergencies (like inspecting storm damage in the dark), with pilots using thermal cameras and spotlights. When done, crews take care to maintain visual situational awareness through additional observers or enhanced lighting on the UAV.
Can drone inspections replace traditional methods?
Drone inspections dramatically reduce the need for certain traditional methods, but they don’t eliminate them entirely. Drones excel at visual and thermal monitoring – they can survey lines and find defects far more efficiently than foot patrols or binoculars. However, drones cannot perform hands-on tasks like tightening hardware, repairing faults, or testing pole integrity. They provide inspection data only. For example, a drone cannot hammer on a pole or physically fix an issue. Utilities still dispatch line crews for maintenance and to handle issues that drones identify. In short, drones augment and improve inspections, finding many problems proactively, but linemen and bucket trucks remain necessary for repairs and certain detailed examinations. The best approach is a hybrid: use drones to cover large areas and pinpoint issues, then send ground teams to address the specific trouble spots.
How do you start a power line inspection drone program?
Implementing a drone inspection program for utilities requires careful planning and adherence to regulations. First, ensure your organization has certified drone pilots (FAA Part 107 in the US) and establish clear operating procedures. It’s wise to start with pilot projects to develop flight protocols, safety checklists, and data management workflows. Successful utility drone programs often have rigorous pre-flight planning (airspace checks, route mapping, weather evaluation), standardized data collection practices, and systematic post-flight analysis routines. You’ll also need to choose the right hardware (drones and sensors suited for your lines) and software integration for analyzing the imagery or LiDAR data. Finally, integration into the maintenance process is key – define how drone findings will translate into work orders for line crews. With training, standard operating procedures, and stakeholder buy-in, a drone program can be launched to improve inspection efficiency and grid reliability.
How do utility companies address privacy concerns when using drones?
Utility companies strive to be transparent and respectful when deploying drones near communities. Powerline inspection drones focus on the electrical infrastructure and rights-of-way, not on private property, and flights are typically conducted at reasonable hours. Many utilities provide advance notice to residents if a drone will be inspecting lines in the area. For example, one utility notifies customers with a phone call before a drone patrol, operates only on weekdays during 8 a.m. to 5 p.m., and avoids flying over homes at night or on weekends. By communicating plans and ensuring drones only capture necessary inspection data (poles, wires, transformers) rather than people or yards, utilities can alleviate most privacy or surveillance worries. Community outreach and clear privacy guidelines are important parts of launching a utility drone inspection initiative.