Complete the form below to receive a custom quote from our Enterprise Sales team. You'll hear from us typically within the hour. We look forward to helping you!
Safer, Smarter Solar Inspections
Solar Panel Inspection Drones
Solar drones give solar companies, utility-scale PV power plant operators, and drone service providers the high-resolution visual and thermal data they need in minutes—all while keeping technicians safely on the ground. By deploying drones for solar panel inspection instead of manual ground inspections, organizations accelerate inspection cycles, maximize energy output, and catch issues before they impact performance—cutting inspection costs at scale.
Megawatt Insights in Minutes
Why Use Drones for Solar Inspections?
Modern solar inspection drones lets asset managers audit every module without shutting down production. Industry field tests show thermal solar drones can scan 1 MW of panels in ≈10 minutes—versus 2-5 hours on foot. One study across four PV sites logged a 97% efficiency boost and ≈ $1,250 savings per MW compared with legacy methods. Other reports peg aerial surveys as up to 70 % faster and 40 % cheaper, often paying for themselves in a single season.
-
Zero-Touch Panel Access:
Keep boots off roofs and racks. A remote solar panel drone inspects live strings from above, eliminating fall risks, electrical contact, and heat-stress exposure for technicians. -
Minute-per-Megawatt Coverage:
Survey days’ worth of modules before lunch. Field data shows drones for solar panel inspection can finish a 900 k-panel site in five days—a 400 % time reduction over manual crews. -
Pixel-Level Thermal Checks:
Find faults invisible to ground checks. High-resolution RGB and radiometric imagery spot micro-cracks, diode failures, and string outages long before they hit performance guarantees—capturing nearly 50 % more defects than handheld sampling -
Yield-Driven Cost Efficiency
Less downtime, higher ROI. By pairing rapid scans with targeted repairs, operators recoup inspection costs quickly and maintain peak output—reporting 30-40 % lower O&M spend and faster warranty validations
Aerial Insights, Safer Outcomes
Use Cases for Powerline Inspection Drones
Commissioning Baseline Surveys
Drones create an IEC-compliant day-zero record, flagging installation defects before PV assets go live.
- Module Alignment Verification: High-resolution imagery confirms row alignment, tilt, and structural straightness to safeguard long-term efficiency.
- Early Defect Detection: Radiometric scans reveal cracked cells or diode failures so EPCs can swap faulty modules pre-energization.
Preventive Maintenance Patrols
Routine drone flights scan entire arrays in minutes, catching issues before they erode output or become safety risks.
- Rapid Hotspot Scouting: ssolar drones sweep megawatt fields quickly, pinpointing emerging hotspots for targeted repairs.
- Trend Analysis Flights: Automated missions capture time-series data that fuels predictive maintenance planning.
Warranty & Insurance Documentation
Timestamped aerial imagery streamlines claims and accelerates approvals when modules underperform or sustain damage.
- Proof-Positive Imagery: High-fidelity RGB and thermal data provide indisputable evidence for warranty or insurance submissions.
- Paperwork Acceleration: Organized drone reports cut back-and-forth with manufacturers and underwriters, speeding reimbursements.
Performance Troubleshooting
Aerial orthomosaics let engineers trace production dips to exact strings, connectors, or shading issues without ground walks.
- String-Level Diagnostics: Thermal panoramas reveal failed strings, connectors, or bypass diodes without dismantling hardware.
- Soiling & Shading Mapping: RGB surveys highlight dirt buildup or shading patterns eroding performance ratios.
Storm & Weather Damage Assessment
Post-event drone surveys quantify hail, wind, or flood damage within hours, guiding rapid response and repair bids.
- Immediate Condition Reports: Fast flights capture cracked glass, lifted modules, and debris across the site for quick prioritization.
- Restoration Prioritization: Detailed maps help crews triage repairs and restore generation swiftly.
Vegetation & Soiling Analysis
Drones identify shading and cleanliness issues that silently sap energy, enabling proactive mitigation.
- Shading Growth Monitoring: Multispectral imagery detects encroaching vegetation before shadows bite into production.
- Soiling Hotspot Identification: RGB orthos spotlight dust, pollen, or droppings so cleaning crews target the right rows.
Find the right UAS for your operations
Solar Inspection packages
We have a wide variety of enterprise drone solutions to help you and your team accomplish your jobs quicker and easier. see our recommended drone packages below or give us a call and get a customized quote for your needs.
Matrice 350 RTK
Fully Powered to Forge Ahead.


An upgraded flagship drone platform, the Matrice 350 RTK sets a new benchmark for the industry. This next-generation drone platform features an all-new video transmission system and control experience, a more efficient battery system, and more comprehensive safety features, as well as robust payload and expansion capabilities
- Up to 55 Minute Flight Time
- 20km Max Transmission Range
- Multiple Cameras
- Higher Payload Compatibility
DJI Matrice 4 Thermal
The Age of Intelligent Flight.


Experience unmatched thermal imaging and intelligent AI capabilities with the DJI Matrice 4 Thermal, designed for precision and performance in challenging environments.
- Ultra-High-Resolution Thermal Imaging
- 112x Hybrid Zoom
- Advanced AI for Real-Time Detection
- 49-Minute Flight Time
- Enhanced Low-Light Operations
Matrice 30T
Power in Portability.
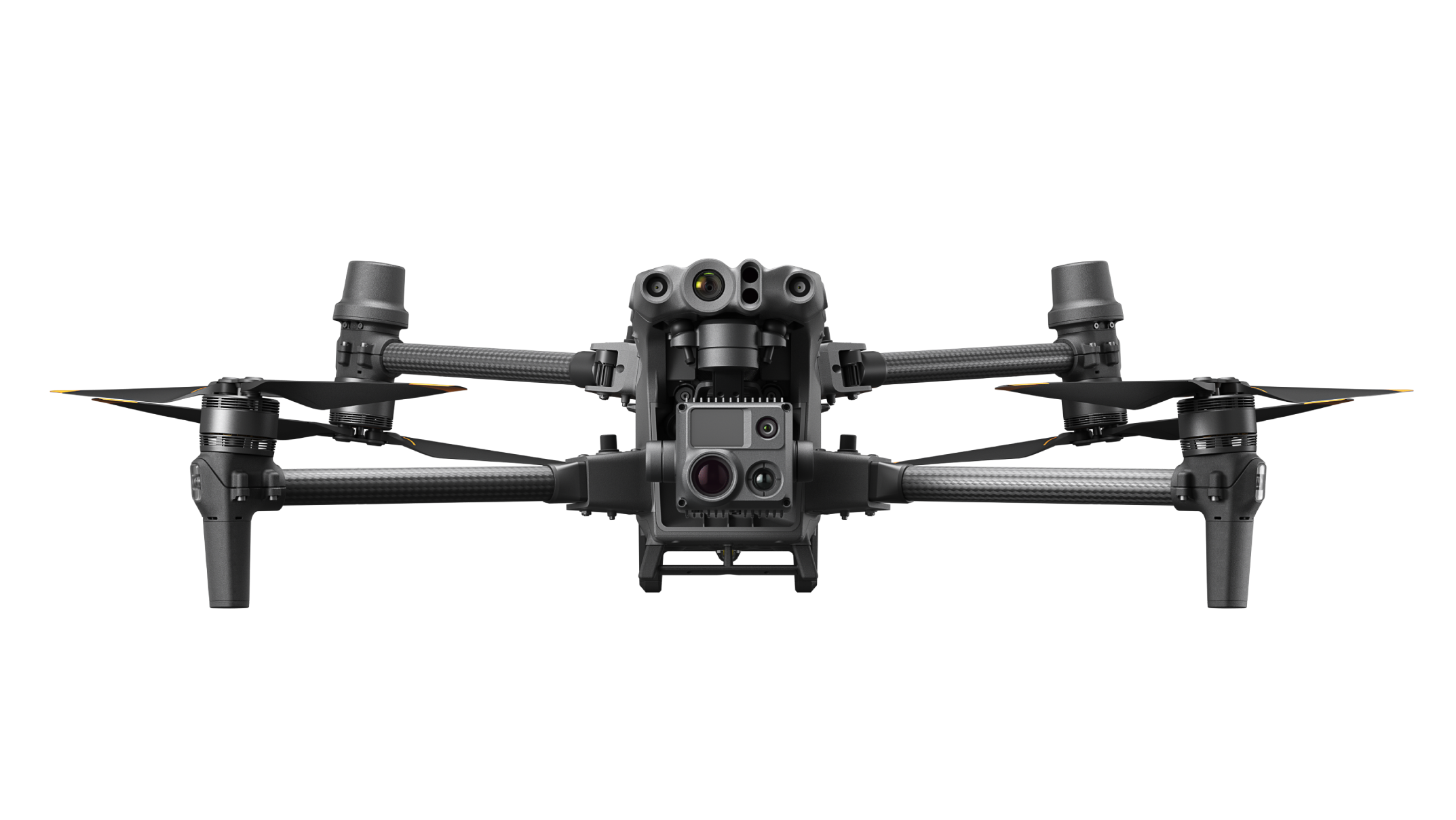
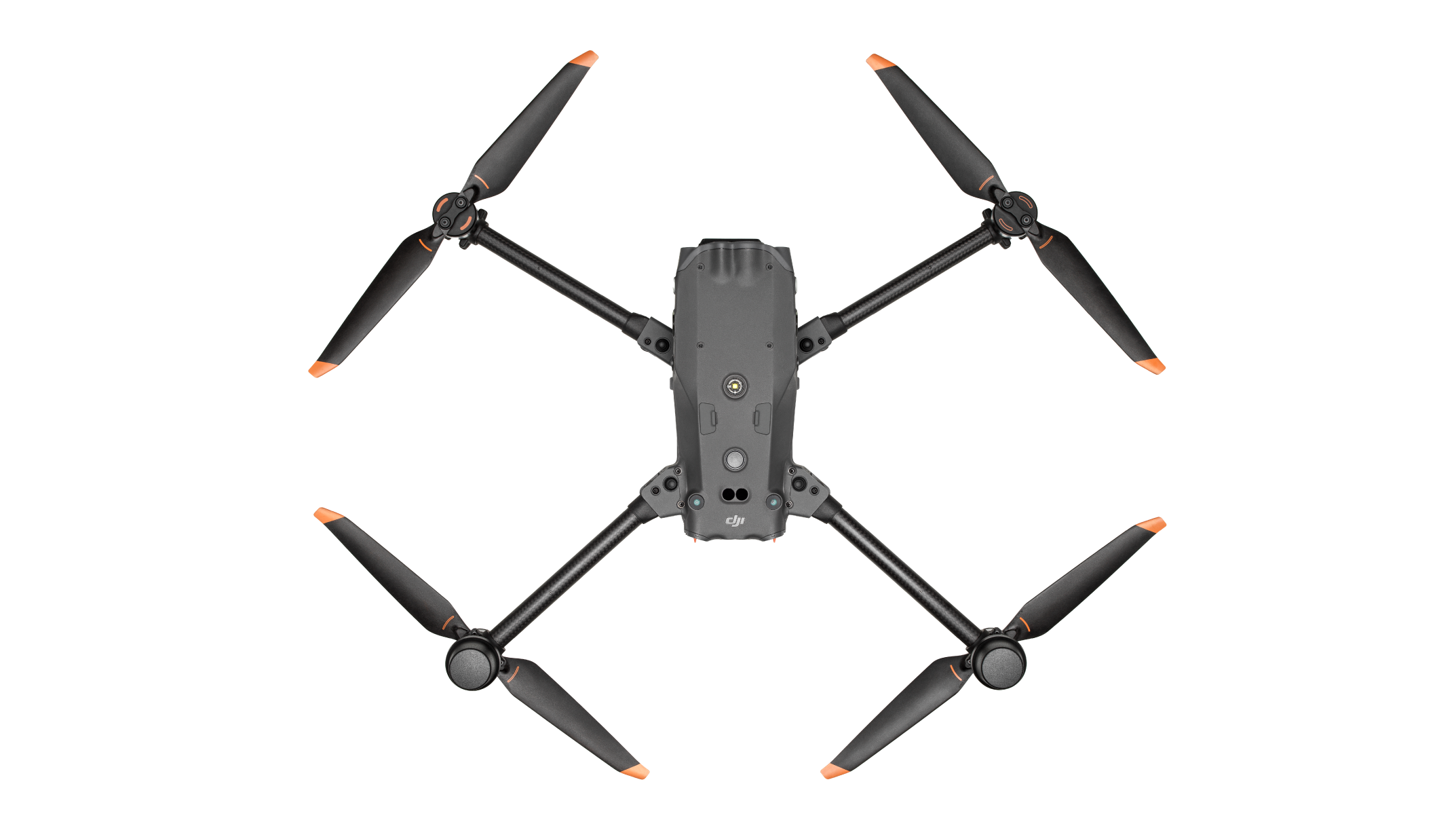
One of DJI's most popular flagship models, the M30T is a weatherproof drone that fits in a backpack and integrates multiple high-performance sensors into one highly capable platform.
- 41 min Flight Time
- 640 × 512 px Thermal Camera
- 12 MP Wide Camera
- 48 MP Zoom Camera
- 5x-16x Optical Zoom
- 0.75 mi. Laser Range Finder
- IP55 Weather Protection
EVO Max 4T XE
Reach New Frontiers.


A feature-packed drone with a 640x512 thermal sensor, 160x hybrid zoom, 10x optical zoom, laser rangefinder, and 4K wide camera. With a flight time of up to 42 minutes and a range of up to 12.4 miles thanks to the SkyLink 3.0 transmission system, it's a choice public safety solution.
- 42 Minute Flight Time
- 640 x 512 Thermal Sensor
- 10x Optical Zoom
- Laser Rangefinder
- 12.4 Mile Transmission Range

Teledyne FLIR SIRAS
Professional Drone With Thermal and Visible Camera Payload


The Teledyne FLIR SIRAS is an IP54-rated professional drone with interchangeable payloads, high-quality visible and thermal imaging, secure onboard data storage, front collision avoidance, and hot-swappable batteries for extended missions.
- 31-Minute Flight Time & Hot-Swappable Batteries
- 640 x 512 Thermal Sensor with 5x Zoom
- 16MP Visible Camera with 128x Zoom
- Front Collision Avoidance Radar up to 30m
- Secure Onboard Data Storage on microSD
- IP54-Rated for Dust and Moisture Resistance
DJI Zenmuse H30T
Unparalleled Vision, Day or Night


The Zenmuse H30T is DJI’s all-weather, multi-sensor flagship payload, integrating a 48 MP wide-angle camera, a 40 MP 34× optical (400× digital) zoom camera, a 1280×1024 radiometric thermal sensor, 3 km laser rangefinder, and NIR auxiliary light. Advanced stabilization and intelligent algorithms deliver crisp, precise imaging in any environment—day or night—for public safety, energy inspection, forestry, and more.
- 48 MP wide camera & 34× optical (400× digital) zoom
- 1280×1024 thermal sensor with High-Res mode & –20 °C to 1600 °C range
- 3 km laser rangefinder for accurate distance & coordinate data
- IP54-rated & –20 °C to 50 °C operation for all-weather reliability
- 3-axis stabilization & advanced algorithms for shake-free zoom footage
DJI Dock 3 with Matrice 4D/4TD
Rise to Any Challenge


DJI Dock 3 drives automated remote operations to new heights with a 10-second takeoff, a rugged IP56 design, and expanded environmental endurance from -30°C to 50°C. Paired with the powerful Matrice 4D/4TD drones, Dock 3 ensures precise, safe flights wherever it’s needed—delivering unmatched efficiency, reliability, and flexibility for diverse industry applications.
- 10-second takeoff for rapid response
- IP56 Ingress Protection & -30°C to 50°C operation
- 12 m/s (≈27 mph) wind resistance
- Up to 54-minute flight time with M4D/4TD
- Vehicle-mounted deployment & remote RTK calibration
- AI object detection & cloud-based analytics with FlightHub 2
Let's get your program started
Ready to build your UAS program?
Get a full, personalized system built for your specific needs. Our expert team can assess your situation, and recommend the best drone system for your organization.
Get a Personalized Quote
Solar Inspection Drones FAQ
What is a drone solar panel inspection, and why is it beneficial?
A drone solar panel inspection is the use of unmanned aerial vehicles (“solar drones”) equipped with cameras to survey photovoltaic (PV) installations. These drones capture detailed thermal and visual images of solar panels to quickly identify issues that might reduce performance. The key benefit is speed and coverage – a drone can scan large solar farms (even hundreds of acres) in a fraction of the time it would take for ground crews . This aerial approach also improves safety by reducing the need for inspectors to physically climb on panels or walk through live arrays. Overall, drone solar inspections are faster, safer, and often more cost-effective than manual methods, while providing high-quality data on the condition of every panel.
What kinds of solar panel issues can drones detect?
Drones equipped with infrared cameras can detect a wide range of PV system problems through the heat signatures on panels. Common issues uncovered during drone solar panel inspections include:
- Hotspots: Overheating cells or modules caused by cell damage, cracks, or faulty interconnections . These appear as bright hot areas in thermal images and can indicate defective cells or solder joints.
- String or Section Failures: Entire strings of panels that are offline or underperforming will show up as cooler (darker) sections in the thermal view, alerting operators to blown fuses, connector failures, or tripped circuits.
- Potential-Induced Degradation (PID): Drones can spot patterns of uneven heating that suggest PID, a condition that gradually reduces output . Affected modules may run hotter or cooler than their neighbors.
- Module Defects: Issues like delamination, damaged bypass diodes, or encapsulant failures often manifest as abnormal heat patterns. High-resolution thermal imagery helps identify subtle module defects that might otherwise go unnoticed.
- Soiling and Shading Effects: While dirt or shade isn’t an internal “fault,” a drone’s thermal scan can highlight panels that are significantly cooler due to heavy soiling or shading (indicating reduced production on those panels).
Additionally, drones capture high-resolution visible-light images, which help confirm physical problems such as cracks, debris, or burned spots on solar panels. By combining thermal and visual data, drones for solar panel inspection give a comprehensive view of panel health, pinpointing both electrical issues and visible damage.
How do drones use thermal imaging to inspect solar panels?
Drones carry special infrared (IR) thermal cameras that detect heat differences across solar panels. During a drone solar inspection, the IR camera measures the surface temperature of each panel or even individual cells. Faulty or electrically stressed components tend to heat up more than normal, creating a thermal “hot spot” that the camera captures as a bright region in the IR image. Conversely, an inactive or underperforming panel may appear cooler than surrounding units.
By flying over the array in systematic patterns, the drone records these thermal images for every module. Analysts (or AI software) then review the images to locate anomalies – for example, a cell-level hot spot indicating a cracked cell, or a cool strip indicating a failed string. Thermal imaging is crucial because most solar panel problems are invisible to the naked eye but show clear heat signatures under operating conditions. In short, solar drones use thermal technology to reveal issues in modules’ performance, allowing maintenance teams to identify and address problems that would be impossible to see in a standard visual inspection.
Can drones inspect solar panels without thermal cameras (using only visual imagery)?
It’s possible to fly a drone over a solar array with just a normal camera, but a solar panel drone inspection without thermal imaging will be very limited. Standard visual photos might spot obvious surface issues (like shattered panels, burning/scorch marks, heavy dirt buildup, or missing modules), but many solar defects leave no visible clues. Problems such as micro-cracks, internal cell damage, or electrical failures typically only show up as heat differences, not as visible damage. For this reason, drones used in solar inspections almost always carry a thermal infrared camera to detect those invisible hot spots and anomalies. In practice, the best approach is to use both: the drone’s thermal camera finds the solar panel issues via heat patterns, and an onboard RGB camera provides high-resolution visual context for each issue.
What is the IEC 62446-3 standard and why is it important for solar drone inspections?
IEC 62446-3 is an international standard that provides guidelines for performing solar PV inspections using infrared drones. In essence, it’s the globally recognized framework for how to conduct drone-based solar panel inspections in a consistent, reliable way. The standard specifies things like the required image resolution, appropriate flight altitude, and even the environmental conditions for thermal inspections.
By following IEC 62446-3, inspectors ensure they are capturing high-quality thermal data that can accurately identify issues such as hot spots, potential-induced degradation (PID), and other module defects. This is important because it standardizes the inspection process across the industry – an IEC-compliant inspection gives asset owners confidence that the results are thorough and credible. In fact, adhering to IEC 62446-3 makes inspections more accurate and reliable, helping to catch subtle faults that a non-standard approach might miss. It also aids in documentation: insurers and warranty providers often prefer or require inspections that meet this standard, since the reports provide the detailed evidence needed for claims.
How can we ensure our drone solar inspections meet IEC 62446-3 compliance?
To conduct an IEC-compliant drone solar inspection, you must plan and execute the survey according to the standard’s key requirements. Here are several steps to ensure compliance:
-
Use the Right Equipment and Resolution: Deploy a drone with a high-resolution radiometric thermal camera so that imagery meets the standard’s resolution criteria. For a detailed IEC inspection, the drone should fly at a low enough altitude to achieve roughly a 3 cm per pixel ground sampling distance (meaning each solar cell is covered by about a 5×5 pixel area) . This often requires a quality 640×512 (or better) IR sensor and an appropriate lens, flying relatively close to the panels to capture fine details.
-
Meet Environmental Conditions: Perform inspections under the environmental guidelines specified by IEC 62446-3. The solar array must be under sufficient load and sunlight – at least 600 W/m² irradiance (roughly a clear sunny day) – to reveal thermal anomalies . Avoid high wind (over ~17 mph or 28 kph) which can cool panels and mask hotspots , and try to inspect when cloud cover is minimal (the standard suggests no more than 2 oktas, i.e. 25% cloud cover ). Also, ensure the panels are clean or minimally soiled; dirt can alter thermal readings and should be removed before inspection if possible.
-
Qualified Personnel: Ensure the operator or thermographer is properly trained. IEC 62446-3 calls for skilled personnel, especially for detailed inspections – typically a certified drone pilot with additional infrared thermography training (for example, a Level I/II Thermographer certification) . Having a technician who understands IR data and the standard’s requirements is crucial for data accuracy and interpreting results.
-
Standardized Data Capture and Reporting: Follow the standard’s procedures for data collection and documentation. Maintain a consistent angle and overlap in images (the drone should view panels at roughly a 90° angle from above, avoiding shallow angles that increase reflectivity ). Capture both thermal images and corresponding visual images of anomalies. After the flight, produce a comprehensive report that tags each detected anomaly with its location, description, and thermal metrics, as IEC compliance requires thorough documentation . Using software that can output reports aligned with IEC guidelines (with details like temperature differentials and classifications of faults) will help fulfill the reporting component of the standard.
What are the best practices for conducting solar panel inspections with drones?
Beyond simply meeting standards, there are established best practices to get the most accurate results from drone solar inspections:
-
Plan Flights Along Panel Rows: Fly the drone in a lawnmower pattern aligned with the solar panel rows. This keeps the camera angle consistent and reduces reflective glare. It’s advised to maintain the camera view as perpendicular as possible to the modules (avoiding angles less than ~30° to the panel surface) to minimize reflections of the sky or sun . Consistent altitude and angle throughout the flight help ensure uniform image quality across the array.
-
Optimize Time of Day and Weather: Conduct inspections under stable, strong sunlight (typically mid-morning to afternoon on a clear day) so that thermal differences are pronounced. Avoid inspections when there’s significant cloud cover or rapidly changing conditions, as moving clouds can cause inconsistent heating. Low wind is important (excess wind cools panels and can hide hot spots), and ideally panels should be free of heavy dust or dirt that could skew thermal readings . We’ll discuss timing more in the next Q&A, but good environmental conditions are fundamental best practice.
-
Use Appropriate Speed and Overlap: Fly at a moderate speed that allows the camera to take crisp, non-blurry images of each section. Many operators use automated flight plans to maintain a steady pace (often a few meters per second) and ensure sufficient overlap between images. Some overlap is useful for cross-checking anomalies from multiple angles, although unlike mapping missions, thermal inspections don’t always require heavy overlap unless creating a stitched thermal map. The goal is to thoroughly cover every panel without rushing – slowing down a bit can vastly improve image clarity for analysis.
-
Calibrate and Verify Sensor Settings: Before flight, calibrate the thermal camera (NUC/calibration routines) and input appropriate settings (like emissivity and reflective temperature, especially if you plan to measure temperatures quantitatively). Use the same settings throughout the flight to keep data consistent. If measuring absolute temperatures, account for environmental factors (emissivity of panels ~0.95, reflected temperature from the sky, etc.) as these affect accuracy. Even if doing a qualitative survey, a well-calibrated camera produces more reliable anomaly detection.
-
Capture Visual Images for Context: Always capture visible-light photos alongside thermal images for any detected anomaly. This is a best practice because it lets you correlate a thermal hotspot with a real-world visual cause (for example, the thermal hotspot might be due to a leaf or bird droppings on the panel, which a visual photo would reveal). Many drone setups have dual cameras (one IR, one RGB) to automatically get both images for each point of interest.
-
Thorough Coverage and Checks: Ensure no areas of the site are missed by cross-verifying flight logs or using software that tracks coverage. For large sites, it may be best practice to break the area into sections and plan separate flights for each, allowing battery changes and easier line-of-sight maintenance. After flights, perform a quality check of the data – make sure the images are clear (no excessive motion blur or out-of-focus shots) and that the number of images aligns with expectations for full coverage. If any gaps are identified, consider re-flying those sections.
When is the best time and weather to conduct a solar farm drone inspection?
The ideal time to perform a drone solar inspection is during clear, sunny conditions when the solar panels are under significant load but not extreme thermal stress. Midday or early afternoon on a sunny day is often optimal, as the sun’s irradiance is high (panels receiving strong sunlight) and the whole system is actively producing power. IEC guidelines suggest at least 600 W/m² of solar irradiance for effective thermal inspections , which typically corresponds to a bright sunny day. At those times, electrical anomalies create distinct heat differences that the drone’s thermal camera can detect. It’s best to avoid early morning or late evening inspections – in those periods, panels may not have warmed up enough, or the low sun angle can cause reflections and uneven heating across modules.
Weather-wise, you want stable conditions: minimal clouds, low wind, and moderate ambient temperature. A near-cloudless sky is important because passing clouds can temporarily cool panels or cause fluctuations in output, complicating the inspection. (The standard recommends no more than 25% cloud cover, as heavy clouds reduce irradiance and could hide issues.) Wind should be limited – strong winds (above ~15–20 mph) can cool down panels and make hot spots less apparent, not to mention it makes drone flight less stable. So picking a day with calm winds is beneficial both for data quality and flight safety.
What flight altitude and speed are recommended for drone solar inspections?
Recommended flight altitude and speed for drone solar panel inspections depend on the level of detail required. For high-resolution, detailed inspections (such as those compliant with IEC 62446-3), drones typically fly relatively low to achieve a fine spatial resolution. In practice, this might mean flying at an altitude that yields about a 3 cm/pixel ground resolution on the panels . For example, using a high-resolution thermal camera, that could correspond to roughly 15–30 meters (50–100 feet) above the panels (the exact altitude varies with camera lens and sensor specs). At this altitude, each solar cell spans multiple thermal pixels, allowing the drone to capture small hotspots or cracks. Flying lower increases detail but also means the drone covers less area per image, so more flight time is needed.
By contrast, a quicker, “simplified” scan might be done at a higher altitude – say 60–120 meters – which covers more panels per image but with less detail. Higher altitude flights are faster but risk missing subtle issues because each camera pixel is covering a larger area. There’s a trade-off: altitude vs. detail. To balance this, many operators choose an altitude in the middle that gives sufficient detail for common faults while still being efficient for coverage.
Do we need to shut down the solar array during a drone inspection?
No – one of the advantages of drone solar inspections is that they are conducted while the solar plant is in operation. In fact, keeping the solar panels energized and producing power is essential for thermal imaging to work properly. Drones find issues by detecting heat differences, and those differences only manifest when current is flowing through the panels. A deactivated or electrically isolated panel won’t generate the telltale hot spots or temperature gradients that indicate faults. Therefore, inspections are typically done under normal or near-normal operating conditions (the standard recommends the system be at least 30% loaded during the test)
How are the data from drone solar inspections processed and analyzed?
Drone solar inspections can generate a large volume of data, especially for big solar farms, so a clear data workflow is crucial. Here’s how the process typically works:
-
Data Collection: During the flight, the drone takes many thermal images (and often corresponding visual images) covering the solar panels. A detailed inspection might result in thousands of images for a large site, each image usually geo-tagged with GPS coordinates. For example, an infrared drone might capture several thousand thermal photos for just a few megawatts of solar, since it’s imaging every module or small group of modules from above. These images are stored on the drone’s onboard memory or transmitted to a ground station as they are taken.
-
Data Upload & Organization: After the flight, the image data is uploaded to a computer or cloud platform for analysis. Specialized solar inspection software is often used to handle the dataset. The software will organize images by their location and time, stitching them into a map or grid layout of the site, or simply aligning them with a site plan. Each image is reviewed for anomalies. Modern tools use AI/machine learning algorithms trained to detect common solar issues (like hot spots or substring outages) in the thermal images, which helps speed up analysis.
-
Anomaly Detection and Tagging: Whether by automated software, human analysts, or a combination of both, each thermal image is analyzed to identify any potential issues. When an anomaly is found, it is “tagged” or marked. Analysts typically classify the type of issue (e.g., cell hot spot, diode failure, string outage, debris/soiling, etc.) and record relevant details (like the temperature delta of a hot cell compared to neighboring cells). Each anomaly is associated with its exact location – often mapping it to a specific panel or string in the solar farm. According to best practices (and IEC standards), every anomaly gets a detailed description in the dataset . This might include the panel ID or coordinates, the severity of the temperature difference, and notes on the likely cause.
-
Visualization and Quality Control: The results are usually visualized in a user-friendly way. For instance, the software might generate an interactive map of the solar farm with icons or markers on each faulty panel . Clicking a marker would show the thermal image and the visible image of that panel, along with the noted issue. A table of anomalies is also created, listing all findings with their details . During this stage, an analyst performs quality control – verifying that the flagged issues are legitimate (filtering out false positives like a momentary cloud shadow or reflection) and ensuring no obvious problem was missed.
-
Reporting: Finally, a report is compiled summarizing the findings. This report typically includes an overview of how many anomalies were found and of what types, often broken down by category (e.g., 10 hot cells, 2 faulty modules, 1 string outage, etc.). It provides visuals – thermal images alongside normal photos for each issue – and their locations. Good reports also estimate the impact of the issues, for instance by approximating how much power loss a hot cell or dead string might cause if left unaddressed . Some advanced reports tie in estimated economic loss (in kWh or dollars) for each anomaly to prioritize fixes . All this information can be delivered as a PDF document, a spreadsheet of issues, and/or through an online dashboard that stakeholders can interact with.
-
Integration: In many cases, the findings can be integrated into the solar asset management or maintenance workflow. For example, the list of anomalies can be imported into a maintenance management system to create work orders for technicians (“replace panel X in row Y” etc.). Some drone inspection platforms directly offer integration or an API to connect with asset management software, streamlining the handoff from data to action.
How are drone inspection results delivered to and used by O&M teams?
The end product of a drone solar inspection is usually a comprehensive report or a data package that the operations & maintenance team can act on. There are a few common formats for delivering the results:
-
Inspection Report (PDF/Document): Many providers will generate a detailed report that includes an executive summary of the inspection and sections listing each finding. For each identified issue, the report might have a table or catalog with the location (array zone, row, and module number, or GPS coordinates), description of the fault, its severity, and images. Typically, you’ll see the thermal image of the panel alongside a normal photo for context . The report often categorizes issues (for example, highlighting which are critical vs. minor anomalies) and may include recommended next steps for repair. It’s not uncommon for the report to quantify the potential impact – e.g., estimating the power loss or revenue loss if that issue stays uncorrected . This helps prioritize fixes.
-
Digital Map/Dashboard: In addition to or instead of a static report, many drone inspection companies provide results via an interactive online platform. This is essentially a map of your solar farm with every detected anomaly geo-referenced (pinned on the map at its exact location) . O&M managers can click on each pin to see what the issue is – complete with thermal and visual images, and details about that finding. This digital delivery is very handy for large sites: technicians can use a tablet or laptop in the field to zoom into the array map and find the exact panel that needs attention. Some platforms allow users to filter by anomaly type (say, show all occurrences of hot cells) or by severity, etc., making it easy to plan maintenance workflows.
-
Data Integration: If the asset owner has their own asset management system or CMMS (Computerized Maintenance Management System), the inspection data can often be exported in a structured format (CSV, Excel, JSON, etc.). This allows the maintenance team to ingest the findings into their system. For instance, each anomaly can become a maintenance ticket. Some advanced solutions have APIs or direct integrations where the anomalies are automatically pushed into a ticketing system with all relevant info attached. This software handoff streamlines moving from “finding a problem” to “assigning it to someone to fix.”
-
Visual Media: All the raw images (thermal and RGB) and perhaps a stitched orthomosaic (an aerial map) of the site might also be delivered. While the O&M team primarily uses the summarized results, having access to the raw data is useful for record-keeping or if they want to do their own analysis on certain areas. For example, engineers might review the thermal imagery in detail to decide if an issue is due to a module fault or something like shade from a tree, etc.
Once delivered, the O&M or asset management team will use the results to guide maintenance actions. Typically, they’ll schedule repair or cleaning for the identified issues.
Is it better to use in-house staff or hire a service for drone solar inspections?
Hiring a Specialized Drone Service: Many solar farm operators choose to outsource inspections to companies that specialize in drone solar panel inspection. The advantages here are that you get experienced pilots and thermographers who already have the proper equipment and know-how. You don’t have to invest upfront in buying drones, thermal cameras, and software or worry about training staff. For one-off or infrequent inspections (say you only need an annual check-up of a few sites), hiring a service can be more cost-effective. The service provider will handle regulatory compliance, data processing, and reporting, delivering a turnkey result. Essentially, you pay per inspection. This is often the preferred route for smaller companies or those with limited solar assets because the volume of work may not justify a full-time drone program.
Building an In-House Drone Team: If your organization manages a large portfolio of solar plants or needs very frequent inspections, developing an in-house drone capability might make sense. With an in-house team, you have flexibility to deploy drones whenever needed (for example, immediately after a storm to check for damage, or more frequent preventative scans). Over time, this can be cost-saving compared to paying external vendors repeatedly. However, there are significant upfront and ongoing commitments: you’ll need to purchase appropriate drone hardware (a professional drone with a thermal camera can be a substantial investment – easily tens of thousands of dollars for a full setup) , train one or more staff members to be licensed drone pilots (and ideally certified thermographers), and maintain the equipment. There’s also the effort of processing and analyzing the data – you might need to acquire software or develop expertise in interpreting thermal images.
What qualifications or training should a drone pilot have for solar inspections?
Conducting drone solar inspections is a technical job, and there are a few key qualifications and skills a pilot should have:
-
Drone Pilot Certification: At minimum, the operator must have any legally required drone license for commercial operations in your region. For example, in the United States a Part 107 Remote Pilot Certificate from the FAA is mandatory for flying drones commercially (which includes solar farm inspections). This ensures the pilot understands aviation rules and can operate safely and legally. Similar certifications exist in other countries (like an A2 CofC or GVC in parts of Europe, etc.). Always verify that your drone pilot is properly licensed to avoid regulatory issues.
-
Thermography Training/Certification: Flying the drone is only part of the task – understanding the thermal data is equally important. It’s highly recommended that the person planning or analyzing solar inspections is trained in infrared thermography. There are professional certifications (e.g., Level I, II, III Thermographer courses) that teach how to interpret thermal images accurately. For detailed IEC-compliant inspections, the standard actually expects a higher level of thermography expertise on the team . A pilot with thermography training will know how to adjust camera settings for emissivity, account for reflections, and distinguish true issues from false indications. They’ll also be better at analyzing the thermal photos and classifying faults.
-
Knowledge of Solar PV Systems: While not a formal certification, it’s extremely helpful if the drone operator (or the accompanying technician) has a solid understanding of solar PV system design and common failure modes. This way, they know what they’re looking at – e.g., recognizing the layout of strings and combiners, understanding what a normal versus abnormal thermal pattern is for panels, and being aware of things like how inverters or optimizers might influence readings. Some issues can have multiple causes, and a bit of solar domain knowledge helps in pinpointing the root cause.
-
Experience with Drones and Data Capture: Solar inspections can be demanding on the drone pilot’s skills. Maneuvering over rows of panels, sometimes in strong sun (which can make it hard to see a tablet screen), and dealing with wind or battery management on large sites – these all require experience. A pilot who has done similar inspections or at least has flight hours in comparable scenarios will be more efficient and less likely to make mistakes. Look for pilots who can show a track record of industrial or utility inspections (not just hobby flying).
-
Attention to Detail and Data Management: The pilot or team should be capable of handling the data properly – that means keeping the images organized, ensuring each image is tagged (many drones geotag automatically), and not losing any files. They should also follow best practices like doing calibration flights, using checklists for equipment, etc.
-
Safety Training: While solar farms are not as hazardous as, say, chemical plants, a pilot should still have basic safety orientation – knowing how to handle lithium batteries safely, how to do an emergency drone shutdown if needed, first aid basics if working in remote solar fields, etc. They should also be aware of site-specific safety protocols, such as wearing PPE if required (helmet, high-vis vest, safety glasses, etc., depending on the site rules), and communications protocol (contacting site operators before flight, etc.).
What safety and legal requirements must be followed when using drones on solar farms?
Using drones for solar farm inspections entails adhering to both aviation regulations and on-site safety practices. Key considerations include:
-
Regulatory Compliance: Legally, any commercial drone operation (which includes inspecting solar panels for a business or utility) must follow the aviation rules of the country. For example, in the U.S. this means compliance with FAA Part 107 regulations. The drone pilot must hold a Part 107 Remote Pilot License , which ensures they understand the rules of the airspace. Regulations typically include maximum altitude restrictions (often 400 feet AGL in the U.S.), maintaining visual line-of-sight with the drone at all times (unless special waivers are obtained), not flying over uninvolved people, and not flying in restricted airspace without permission. Before flying at a new solar site, the pilot should check airspace maps – some solar farms are in rural open areas which is usually unrestricted airspace, but if a site is near an airport or in controlled airspace, special authorization might be needed for drone flights.
-
On-Site Permissions: Ensure that you have permission to fly at the solar farm from the asset owner or site manager. This might seem obvious if you yourself are the asset owner, but if the site is third-party owned or operated, coordination is needed. Often, a site will require a permit-to-work or at least a notification that a drone flight is occurring, so that all personnel on site are aware (and so that they don’t confuse the drone with an intrusion or something unexpected).
-
Pre-Flight Safety Checks: The drone operator should perform thorough pre-flight checks. This includes inspecting the drone hardware (propellers, battery levels, sensors) for any issues, confirming GPS lock and home point, and making sure the weather conditions are safe (no sudden high winds, storm incoming, etc.). They should also establish emergency procedures, like identifying a safe crash zone in case of loss of control, and ensure the return-to-home function is properly set (so if the drone loses signal or is low on battery, it will safely return or land where intended, not on the panels).
-
Distance from Panels and Structures: While drones can fly close to panels, it’s wise to maintain a buffer to avoid any chance of collision. Typically flying 10–20 feet (3–6 meters) above the panels is sufficient to get good thermal imagery while providing a margin for safety. The pilot should be cautious around any structures like weather stations, substations, or tracker machinery that protrudes from the array, as well as avoid contact with fencing or power lines at the site. Modern drones often have obstacle sensing, but solar panels can be tricky (they’re flat and sometimes the sensors may not register the uniform surface well), so manual caution is important.
-
Use of Visual Observers: If the flight area is broad or complex, it’s a good practice (and in some scenarios a legal requirement) to have a second person as a visual observer. This person helps keep eyes on the drone if the pilot is focused on the screen, and expands the visual coverage if the drone flies far. For very large solar farms, maintaining line-of-sight might require moving in segments or having multiple observers.
-
Weather and Environmental Safety: Avoid flying in unsafe conditions. This includes high winds that could cause a crash, lightning or storms in the area, or extreme temperatures outside the drone’s operating range. Also, never fly in rain or heavy moisture when inspecting solar farms – not only would the data be poor (and the drone potentially damaged), but it risks the drone failing over the panels.
-
Crowd and Property Safety: Solar farms are usually not crowded places, but if there are workers on the site, coordinate to ensure you’re not flying over them. If maintenance crews are working on a specific section of the array, you might schedule the drone flights in that area when they are not directly under the drone to abide by the “no flight over people” rule (unless using a drone certified for operations over people, which most are not). Additionally, respect privacy and property boundaries – only fly over the solar farm property (do not inadvertently drift over neighboring homes or farms).
-
Insurance: While not a “law” in many areas, carrying drone liability insurance is effectively a requirement for commercial operations. It protects against any potential damage. For instance, on the off chance a drone did malfunction and crash into a panel (rare, but possible), insurance would cover the cost of that panel replacement. Many solar operators will insist any contractor has insurance, and if it’s your own drone, you should secure insurance for peace of mind.
-
Emergency Procedures: The pilot should have a plan for how to handle emergencies. This includes things like what to do if a drone loses GPS or control (usually: let it hover or slowly attempt to descend in a safe spot), and when to use the “kill switch” (stopping motors mid-air) – which generally you avoid unless the drone is in a dangerous uncontrolled state. If a drone does go down, the team should know how to respond safely, especially if it lands on live electrical equipment (generally drones are small and won’t harm the solar equipment significantly, but one should follow lockout/tagout if retrieving pieces from near live gear, etc.).
How long does it take to inspect a solar power plant with drones?
Drone inspections are significantly faster than manual inspections. The exact time depends on the size of the solar installation and the level of detail required, but we can give some typical examples. For a utility-scale solar farm, a single drone team can often survey several megawatts of capacity per hour under good conditions. One study showed that a 5 MW solar farm, which would require roughly 125 man-hours to inspect on foot, could be covered by a drone in only about 1 hour . Similarly, a 50 MW site that might take a ground crew weeks to examine (well over a thousand labor hours) was completed in around 10 hours of flight time by a drone.
n practical terms, a standard quadcopter with a thermal camera can typically cover on the order of 10–20 MW in a day (with a skilled crew and multiple battery swaps), depending on how the site is laid out. If the site is compact and the drone can fly continuous lawnmower patterns, coverage is maximized. If the site is segmented or has obstacles, it might slow down slightly. Also, if performing a very detailed inspection (flying lower for higher resolution), the drone has to take more images and fly more passes, which can slow things down compared to a quick scan. For instance, an IEC-compliant detailed scan might deliberately fly slower and lower, so the same size site could take longer than a simplified scan.
Here are some rough figures to illustrate timeframes:
-
Small Commercial Array (e.g. 0.5 MW on a rooftop): A drone can finish this in minutes – maybe 10–20 minutes of flight, plus setup time – very quick.
-
5 MW Solar Farm: As noted, roughly an hour give or take, including battery changes and some image checks. This could be a single flight if the drone has good endurance, or a couple of shorter flights.
-
20 MW Solar Farm: On the order of 2–4 hours. Possibly a morning’s work for one team.
-
100 MW Solar Farm: Typically this might take a full day or even two days for one drone team. If the drone can cover ~15–20 MW per day safely, you’d break 100 MW into segments. Some experienced teams have reported doing ~100 MW in a day by optimizing everything and using multiple batteries, but that’s hustling and usually with more than one crew.
How often should solar panel systems be inspected using drones?
As a general guide, yearly is the minimum for proactive maintenance. Industry sources note that if you’re inspecting once per year with drones, you’re essentially at the current standard practice for preventative maintenance. Older systems or those that have shown reliability issues might benefit from stepping up frequency to twice a year or more. Newer systems might be fine with annual checks since the likelihood of issues is lower early on (though initial inspections are important to catch any installation mistakes).
Can drones be used to inspect rooftop solar panel installations?
Yes, drones can be effectively used to inspect rooftop solar installations, not just large ground-mounted solar farms. Many solar O&M providers use drones for commercial and industrial rooftop PV systems as a safer and quicker alternative to walking on the roof. The principle is the same: a drone equipped with a thermal camera can fly over a roof and scan the panels for hot spots and anomalies.
What are the limitations or challenges of using drones for solar inspections?
While drone inspections are extremely useful, there are some limitations and challenges to be aware of:
-
Weather and Environmental Dependence: Drones can’t be flown in all weather conditions, and thermal inspections in particular require certain environmental criteria. High winds can be a challenge – not only is it unsafe to fly if winds are too strong, but wind cools down the solar panels which can mask thermal anomalies or make temperature differences less detectable . Rain or heavy dust in the air will also preclude flying and can damage equipment. Thermal inspections need sunlight, so you can’t do them at night (for solar PV) and cloudy days reduce the effectiveness of finding hot spots, since if irradiance drops too low, even bad panels won’t show much temperature difference. Essentially, you have to pick your window: a clear, calm day. Very high ambient temperatures can also reduce thermal contrast between good and bad panels, making it a bit harder to spot issues, though with a good camera you can adjust for that. These dependencies mean sometimes an inspection has to be rescheduled due to weather, which is a logistical challenge.
-
Data Volume and Analysis: A thorough drone inspection of a large solar farm generates thousands upon thousands of images. For example, a detailed IEC-compliant survey might produce a massive set of high-res thermal images (possibly on the order of ~6,000 images per megawatt for very detailed scans, meaning a 50 MW site could yield 300,000 images). Handling this volume of data is a challenge. It requires advanced software to process and analyze; doing it manually would be extremely time-consuming and prone to human error (imagine trying to look through hundreds of thousands of images without software help). Even with good software, one must ensure anomalies are correctly identified and not missed or double-counted. The post-processing workload and need for effective data management is something to consider – it’s often solved by using AI-driven analysis tools, but those come with their own cost/learning curve. Smaller sites don’t have this issue as much, but for utility-scale, data overload is a real challenge .
-
Battery Life and Range: Drones have limited flight times (commonly 20–30 minutes per battery for high-end drones carrying thermal cameras). On a very large site, the pilot will need to do multiple flights to cover everything, swapping batteries in between. If the site is spread out over many acres, the drone might need to return home and take off from different points to stay within line-of-sight or to be efficient. This means inspections have to be carefully planned and can take multiple hours or days, as the drone can’t just fly non-stop. It’s still way faster than manual, but one should plan for battery management and possibly bring multiple drones or rapid charging setups to minimize downtime.
-
Line-of-Sight and Regulatory Limits: For expansive solar farms, keeping the drone within visual line-of-sight (a common legal requirement) might mean the pilot has to move or use multiple observers, which complicates operations. Some companies are obtaining waivers for beyond visual line-of-sight (BVLOS) flights for solar farms, which will ease this, but such approvals are still not ubiquitous. Also, airspace restrictions might limit flights in some sites near airports or sensitive areas – getting waivers or permissions adds an administrative challenge.
-
Detection Limitations: Drones with thermal cameras excel at finding many types of faults, but they’re not a 100% catch-all for every single issue. For instance, very subtle degradation or soiling that uniformly affects a panel may not create a strong thermal signature and could be overlooked. If a panel’s entire output is slightly down (maybe due to light soiling), it might still appear uniformly warm like its neighbors. Drones typically catch relative issues (one panel hotter/colder than the rest). Also, some failures might only show under certain conditions that aren’t present during the inspection. For example, a marginal connection might only heat up when a very high current passes; if you inspect on a mild day, it might not manifest. In practice, drones find the majority of significant issues, but tiny micro-cracks that haven’t caused thermal differences yet or very small output degradations might slip through. That said, as long as the inspection meets IEC specs (good resolution and conditions), it should even pick up subtle faults like micro-cracks causing slight heating . The risk is more if someone tries to do a quick, high-altitude scan – then they might miss things because of insufficient detail .
-
Interpretation and False Positives: Interpreting thermal images can sometimes be tricky. Not every hot spot is a solar cell defect – for example, a bird dropping on a panel will create a hot spot (because it shades part of a cell and causes that cell to heat up). The drone might flag that as a “hot cell,” but the fix is just cleaning. Similarly, an observed cool panel could be offline intentionally (maintenance or a known issue) rather than a failure that just happened. In other words, context matters. The challenge is having knowledgeable people or intelligent software to distinguish real problems from benign anomalies. The IEC standard and best practices mitigate this by requiring visual confirmation images and proper classification, but it’s still possible to get false positives/negatives if one isn’t careful. That’s why having skilled analysts or good AI is important.
-
Operational Logistics: There are some basic practical challenges too: making sure you have access to the site (some solar farms are remote, locked, require safety orientations); dealing with dust or heat on-site (the pilot might be standing out in a field under the sun — human endurance factors); ensuring the drone and tablets don’t overheat in hot climates; coordinating with site operations (so that sprinklers or trackers or other site systems don’t interfere during the flight). While these are manageable, they do mean an inspection is not just “show up and fly” – it requires prep and sometimes travel to very remote locations with all your gear.
-
Cost and Expertise: While cheaper than some manual methods, drone inspections still require upfront investment in equipment or hiring experts. Smaller solar operators might find it challenging to justify the expense unless they pool inspections or hire third-party services on an as-needed basis. There is a learning curve associated with using drones and interpreting thermal data, which means you need skilled personnel – not every solar technician is immediately equipped to also be a drone thermographer without training.
How accurate are drone solar inspections compared to traditional methods?
Drone-based solar inspections, when done with high-quality equipment and proper methodology, have proven to be extremely accurate – on par with traditional electrical testing in identifying issues, and in some cases even more comprehensive due to 100% coverage. Several studies and field comparisons have demonstrated this high accuracy:
-
Detection Accuracy: In one notable comparison, a drone thermal inspection’s results were 99% in agreement with a manual electrical inspection of a solar farm . In that case, the manual inspection took two days (involving methods like IV-curve tracing or hand-held IR) while the drone found the same issues in about two hours, with virtually no discrepancies in what was identified. Similarly, industry metrics often cite that drones can achieve around 95–99% accuracy in fault detection versus traditional methods, assuming the drone survey is executed under proper conditions .
-
Coverage vs Sampling: One aspect of accuracy is that drones examine the entire array, whereas traditional manual inspections often sample a subset of panels (because checking every panel with a handheld device is too time-consuming). For instance, it’s common in manual maintenance to test maybe 10-20% of panels and assume the rest are okay, which inherently can miss problems. Drones, by covering everything, can catch issues that a sampling approach would statistically miss . So in terms of thoroughness, drones provide a more complete picture. A faulty panel hiding in the back of a row might never get checked manually, but the drone will likely see it since it images every panel from above.
-
Temperature Measurement vs Electrical Readings: Traditional methods like IV curve tracing give very precise electrical performance data, which drones do not directly provide. A thermal image doesn’t tell you the exact power output of a panel, but it tells you if there’s a thermal anomaly that correlates to a fault. If the question of accuracy is about “did we correctly identify faulty panels?”, drones are excellent at that. If the question is “did we measure the exact power loss?”, then you might still complement with some electrical tests. However, many drone platforms now integrate estimated metrics (they can infer, for example, that a hot cell might lead to X% power loss). In identifying the presence and location of faults, which is the main goal of inspection, drones are very accurate.
-
False Negatives/Positives: With a proper high-resolution thermal camera and adherence to the IEC standards (like good irradiance, appropriate flight altitude, etc.), the likelihood of false negatives (i.e., the drone missing an existing problem) is low. Extremely subtle issues might evade detection (as mentioned before, something like uniformly degraded panels without hot spots might not raise a flag). But serious issues like cracked cells, disconnected strings, failing diodes, etc., almost always create a thermal signature that the drone will catch. The key is resolution – a compliant inspection that resolves cell-level detail will see even small hot spots , whereas a quick-and-dirty low-res flyover might miss minor ones. False positives (flagging something as a problem when it’s not an equipment fault) can occur, but those are typically things like dirt or shade, which a skilled analyst can often recognize and filter out, especially if visual images are reviewed in tandem.
-
Consistent Quality: Drones also bring consistency. Human inspectors can have variability in how well they catch things (fatigue, skill level, etc.), but a drone with an automated flight and a systematic process will consistently capture the necessary data. This consistency translates into reliable detection rates across an entire site and across multiple sites. If the drone inspection procedure is standardized, you get uniform results (which is part of why standards like IEC 62446-3 exist – to ensure accuracy and consistency).
-
Industry Acceptance: The accuracy of drone thermography has reached the point that many insurance companies and warranty providers accept drone IR reports as evidence for claims. They trust that a properly done drone inspection will accurately document issues . This indicates confidence that the technology finds what needs to be found.